双螺杆热熔挤出机是高分子材料加工(如塑料共混、造粒、反应挤出)的核心设备,其运行稳定性直接影响产品质量与生产效率。由于长期处于高温(150 - 350℃)、高压(螺杆压力可达20 - 50MPa)及高剪切环境,设备的维护保养与故障排除需结合机械结构、热力学特性及工艺需求进行系统性管理。以下从维护保养规范与常见故障处理两方面展开详细分析。
一、双螺杆热熔挤出机的维护保养规范
1. 日常操作维护:预防性管理的关键
日常维护是减少设备故障的基础,需在每次开机前、运行中及停机后进行标准化操作。
开机前检查
润滑系统:检查齿轮箱、轴承座的润滑油液位(油标中线以上),油质需清澈无杂质(若发黑或含金属颗粒需立即更换);手动盘车确认螺杆转动灵活,无卡滞异响。
加热系统:检查加热圈绝缘性能(用万用表测量电阻值,正常>10MΩ),确认温控仪表设定值与工艺要求一致(误差<±2℃);预热阶段需缓慢升温(升温速率≤50℃/h),避免热应力导致机筒变形。
进料系统:清理料斗内残留物料(防止结块堵塞),检查强制喂料器的螺杆与皮带传动是否正常,避免进料不均引发螺杆扭矩波动。
运行中监控
温度稳定性:通过温控仪表实时监测机筒各段温度(如加料段、压缩段、均化段),波动范围需控制在±3℃内;若某段温度持续偏高(超过设定值5℃以上),需检查加热圈是否局部短路或冷却水路是否堵塞。
压力与扭矩:观察挤出机主电机电流(正常范围为额定值的60% - 80%)及压力传感器数据(螺杆压力≤40MPa),若电流骤增或压力波动剧烈,可能因物料塑化不良或螺杆磨损导致。
物料状态:通过视窗观察熔体流动性(应均匀、无气泡或未熔颗粒),若出现“架桥”(物料在料斗内堆积不下落)或“过热碳化”(熔体发黄、有焦味),需及时调整进料速度或停机清理。
停机后保养
清机操作:生产不同配方物料时需清机(避免交叉污染),先排空机筒内剩余物料,再用高粘度硅油或专用清洗料(如PP清洗料)以低速(螺杆转速≤10rpm)挤出,直至熔体无杂质;高温段机筒需持续保温(温度≥180℃)防止残留物料固化。
冷却系统维护:关闭加热系统后,启动冷却水循环(流量≥2m³/h),带走机筒与螺杆残余热量;检查冷却水管路是否漏水(重点检查法兰连接处及软管接头),避免水渗入电气柜引发短路。
表面清洁:用软布擦拭设备表面(禁用钢丝球或硬质刷子),清除油污与粉尘;拆卸防护罩检查内部是否有异物(如金属屑、塑料碎片),防止进入传动系统。
2. 定期深度保养:延长设备寿命的核心
定期保养需根据设备运行时长(通常以2000 - 3000小时为周期)进行系统性维护,重点关注易损件与关键部件。
螺杆与机筒的检测与修复
磨损检测:拆卸螺杆后,用千分尺测量螺纹外径(重点检查压缩段与均化段),磨损量>0.5mm需修复或更换;机筒内孔用内径千分表检测,圆度误差>0.1mm或表面粗糙度Ra>1.6μm时需镗孔修复。
表面处理:轻微磨损的螺杆可采用等离子喷涂(涂层材料为WC - Co硬质合金)或激光熔覆修复,恢复尺寸精度(涂层厚度0.2 - 0.5mm);机筒内壁若出现划痕或腐蚀坑,需通过珩磨加工(表面粗糙度Ra≤0.8μm)提升光洁度。
传动系统的维护
齿轮箱:更换齿轮油(ISO VG150或VG220,根据工况选择),清洗磁性滤网(清除金属磨屑);检查齿轮啮合间隙(侧隙≤0.1mm,顶隙≤0.2mm),若齿面出现点蚀或胶合需更换齿轮组。
轴承与密封件:拆卸轴承座检查滚子与内外圈磨损情况(若出现麻点或剥落需更换);更换机械密封件(如机筒与螺杆间的唇形密封圈),确保密封面无划痕(密封压力≥0.3MPa)。
加热与冷却系统的检修
加热圈:检测功率稳定性(用功率分析仪测量,偏差<5%),更换老化绝缘层(云母片或陶瓷纤维);校准温控仪表(与标准温度计对比,误差<±1℃)。
冷却水路:清洗过滤器(清除水垢与杂质),检测水泵扬程(≥0.3MPa)与流量(≥设计值的90%);对长期使用的铜管或不锈钢管路进行涡流探伤(检测壁厚减薄量,减薄>20%需更换)。
3. 长期停机的特殊保养
若设备需停机超过1个月,需采取防锈、防潮措施:
拆卸螺杆与机筒,涂抹防锈油(如二硫化钼锂基脂)后包裹塑料薄膜;
清空齿轮箱与液压油箱,注入保护油(如含缓蚀剂的矿物油);
关闭电气柜门,放置干燥剂(如硅胶包)并定期更换(每2周一次)。
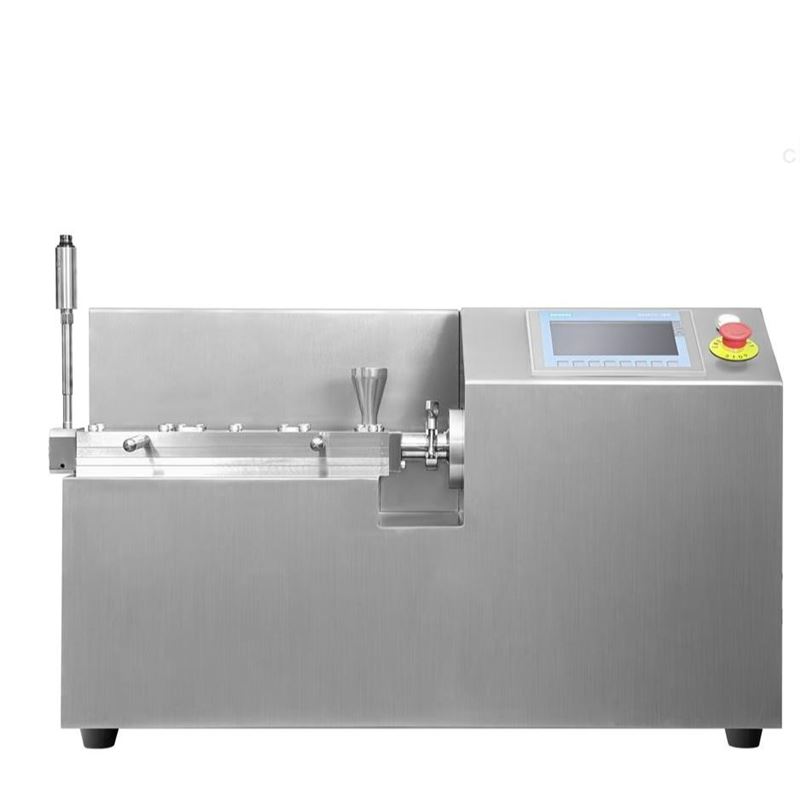
二、双螺杆热熔挤出机的常见故障与排除方法
1. 机械类故障:传动与结构问题
故障现象:螺杆扭矩异常升高(电机电流骤增)
可能原因:物料塑化不良(如含水分或未干燥)、螺杆与机筒间隙过小(磨损后未调整)、异物进入螺槽(如金属杂质)。
排除方法:检查进料物料的含水率(需<0.02%),增加烘干时间(如80℃热风干燥4小时);拆卸螺杆与机筒,测量间隙(正常值为0.1 - 0.3mm),若间隙<0.1mm需更换螺杆或修复机筒;检查料斗筛网是否破损,加装磁力架(吸附金属颗粒)。
故障现象:齿轮箱异响(周期性撞击声)
可能原因:齿轮磨损(齿面点蚀或胶合)、轴承损坏(滚子破裂)、润滑不足(油量不足或油质差)。
排除方法:停机后拆开齿轮箱盖,检查齿轮啮合面(若有点蚀深度>0.1mm需更换齿轮组);拆卸轴承座,用听诊器检测滚子转动声音(若出现“沙沙”声需更换轴承);补充齿轮油至油标中线以上,更换老化滤芯。
2. 热力学类故障:温度与压力异常
故障现象:机筒某段温度失控(持续升高或无法升温)
可能原因:加热圈局部短路(绝缘层破损)、温控仪表故障(传感器漂移)、冷却水路堵塞(水管结垢或阀门未开)。
排除方法:用万用表测量加热圈电阻值(若<5MΩ需更换);校准温控仪表(与标准热电偶对比,误差>±3℃需调整或更换);检查冷却水管路(用高压水枪冲洗过滤器,清除水垢)。
故障现象:熔体压力波动大(压力表指针频繁摆动)
可能原因:螺杆转速不稳定(变频器故障)、物料进料不均(料斗架桥或喂料器故障)、机筒排气口堵塞(挥发分无法排出)。
排除方法:检查变频器输出频率(正常波动范围<±2Hz),重启或更换变频器;清理料斗内结块物料(用木棒轻敲内壁),检查强制喂料器皮带张力(张紧力≥50N);拆卸机筒排气口滤网(清除塑料熔体残留)。
3. 工艺类故障:产品质量问题
故障现象:挤出制品表面粗糙(有气泡或条纹)
可能原因:物料塑化不充分(温度偏低或螺杆剪切不足)、熔体中含气泡(物料含水分或挥发分)、模具温度不均(冷却不充分)。
排除方法:提高机筒温度(如加料段提高10 - 15℃),调整螺杆转速(增加剪切强度);检查物料干燥工艺(如PET需在150℃下干燥4小时);清理模具冷却水道(确保水流均匀,温差<5℃)。
故障现象:制品颜色不均(出现色斑或条纹)
可能原因:色母粒分散不良(螺杆混合能力不足)、加料顺序错误(色母粒未与基料充分预混)、机筒内壁残留旧颜色物料。
排除方法:更换高剪切螺杆元件(如捏合块或齿形盘),提高混合效率;采用预混工艺(色母粒与基料按比例在高速混合机中搅拌10分钟);清机(用清洗料挤出至熔体无色差)。
三、维护保养与故障排除的核心原则
预防为主:通过日常巡检与定期保养降低故障发生率,避免“带病运行”;
数据驱动:记录温度、压力、电流等关键参数的历史数据(如建立Excel台账),通过趋势分析预判潜在问题;
专业操作:故障排除需结合设备原理与工艺知识,避免盲目拆卸(如螺杆拆卸需使用专用工具,防止螺纹损伤)。
结语
双螺杆热熔挤出机的维护保养与故障排除是保障其高效运行的关键环节。通过标准化的日常维护、周期性的深度保养及快速精准的故障处理,可显著延长设备寿命、提升产品质量稳定性,并降低生产成本。未来,随着智能化监测技术(如在线磨损检测传感器、AI故障预测模型)的应用,挤出机的维护管理将向更高效、更精准的方向发展。